Mastering PLC Programming: A Comprehensive Guide
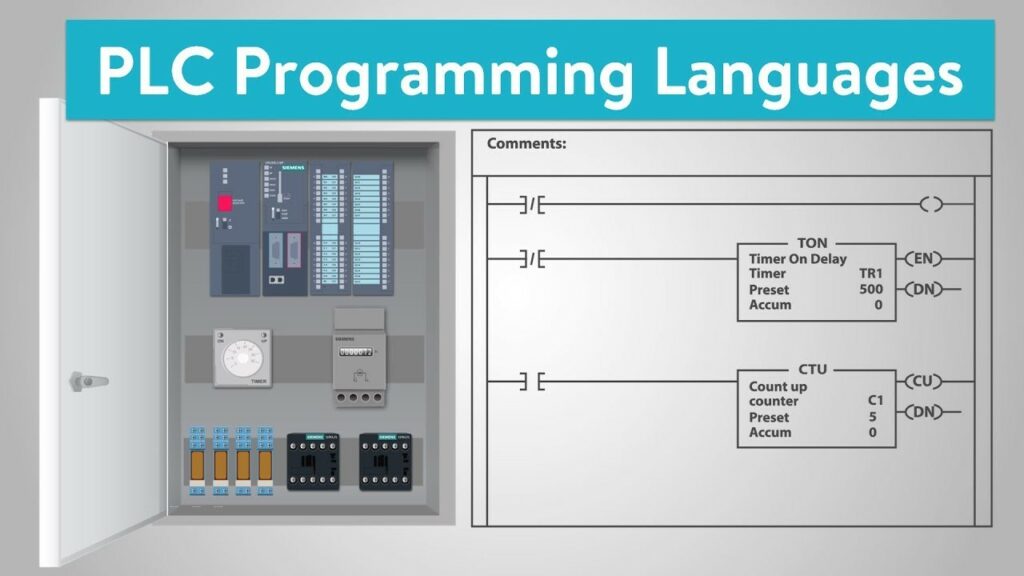
Introduction: Programmable Logic Controllers (PLCs) are essential components in industrial automation systems, controlling machinery and processes in manufacturing, utilities, and other industries. PLC programming involves creating logic programs to automate tasks, monitor inputs, and control outputs. In this extensive guide, we’ll explore the intricacies of PLC programming, covering everything from basic concepts and programming languages to advanced techniques and real-world applications.
Section 1: Introduction to PLC Programming 1.1 Overview of Programmable Logic Controllers: Programmable Logic Controllers (PLCs) are specialized industrial computers designed to control electromechanical processes and machinery. PLCs are widely used in manufacturing, automotive, aerospace, and other industries for tasks such as machine control, process automation, and production monitoring. PLC programming involves creating ladder logic, function block diagrams, or structured text programs to define the behavior of the control system.
1.2 Importance of PLC Programming: PLC programming is critical for automating industrial processes, improving productivity, and ensuring consistent quality in manufacturing operations. By programming PLCs, engineers can create flexible and scalable control systems that respond to changing production requirements and optimize resource utilization. PLC programming also plays a vital role in ensuring safety, reliability, and compliance with industry standards and regulations.
Section 2: Basic Concepts of PLC Programming 2.1 PLC Architecture: PLCs consist of three main components: the CPU (central processing unit), input modules, and output modules. The CPU executes the control program and coordinates communication between input and output devices. Input modules interface with sensors and switches to monitor the status of machine inputs, while output modules control actuators and devices to perform desired actions.
2.2 Programming Languages: PLC programming can be done using various programming languages, including ladder logic, function block diagrams (FBD), structured text (ST), and sequential function charts (SFC). Ladder logic is the most common programming language for PLCs, resembling electrical relay logic diagrams. Function block diagrams represent functions and operations as interconnected blocks, while structured text provides a text-based programming environment similar to traditional programming languages.
Section 3: Ladder Logic Programming 3.1 Ladder Logic Basics: Ladder logic is a graphical programming language used to create PLC programs based on relay ladder diagrams. Ladder logic programs consist of rungs, which represent logical operations performed on input signals to produce output signals. Each rung contains input contacts, which represent sensor inputs or switch states, and output coils, which control actuators or devices.
3.2 Ladder Logic Instructions: Ladder logic programs use a variety of instructions to implement logical operations, arithmetic calculations, and control functions. Common ladder logic instructions include AND, OR, NOT, timers, counters, compare instructions, and arithmetic operations. These instructions allow engineers to create complex control algorithms and sequences to meet specific application requirements.
Section 4: Advanced PLC Programming Techniques 4.1 Sequential Function Charts (SFC): Sequential Function Charts (SFC) are a graphical programming language used to model complex control sequences and state-based logic. SFC programs consist of interconnected steps, which represent different states or stages in a control process. Engineers can use SFC to design sequential control systems, state machines, and process control applications with clear, hierarchical structures.
4.2 Function Block Diagrams (FBD): Function Block Diagrams (FBD) are another graphical programming language used in PLC programming. FBD programs consist of interconnected function blocks, each representing a specific function or operation. Engineers can use FBD to create modular, reusable code blocks and implement complex control algorithms using a visual, block-based programming environment.
Section 5: Real-World Applications and Case Studies 5.1 Manufacturing Automation: PLCs are extensively used in manufacturing automation for controlling production processes, assembly lines, and robotic systems. Engineers use PLC programming to automate tasks such as material handling, sorting, packaging, and quality control. PLC-controlled systems improve efficiency, reduce errors, and enable real-time monitoring and optimization of manufacturing operations.
5.2 Building Automation: In building automation systems, PLCs are used to control HVAC (heating, ventilation, and air conditioning) systems, lighting, security, and access control. PLC programming allows engineers to create intelligent building management systems that optimize energy usage, enhance occupant comfort, and ensure safety and security.
Section 6: PLC Programming Best Practices 6.1 Modular Programming: Modular programming is a best practice in PLC programming, involving breaking down complex control algorithms into smaller, reusable modules. Engineers can create modular code blocks for common functions and operations, such as motor control, PID loops, and data logging. Modular programming improves code readability, maintainability, and scalability, making it easier to debug and update PLC programs.
6.2 Documentation and Comments: Documenting PLC programs and adding comments is essential for ensuring code clarity and readability. Engineers should provide detailed descriptions of program logic, input/output assignments, and function blocks. Comments should explain the purpose of each section of code, document changes and revisions, and provide troubleshooting information for maintenance personnel.
Section 7: PLC Programming Tools and Resources 7.1 PLC Programming Software: There are many software tools available for PLC programming, including vendor-specific programming environments such as Siemens TIA Portal, Rockwell Studio 5000, and Schneider Electric Unity Pro. These software platforms provide integrated development environments (IDEs) for creating, testing, and debugging PLC programs, as well as simulation tools for virtual testing of control logic.
7.2 PLC Programming Resources: Engineers can access a wealth of resources and training materials to learn PLC programming, including online tutorials, books, forums, and training courses. Many PLC manufacturers offer free online resources, technical documentation, and support forums for their products. Additionally, there are specialized training programs and certifications available for PLC programming, covering topics such as ladder logic, function blocks, and industrial automation.
Conclusion: PLC programming is a critical skill for engineers and technicians working in industrial automation and control systems. By mastering the techniques and best practices outlined in this guide, engineers can create efficient, reliable PLC programs that automate processes, optimize performance, and improve productivity in a wide range of industrial applications. With the right tools, resources, and expertise, PLC programming enables engineers to design and deploy innovative control solutions that drive efficiency, safety, and competitiveness in today’s manufacturing and industrial environments.